Encapsulated Polystyrene Infill, London
15/06/2022
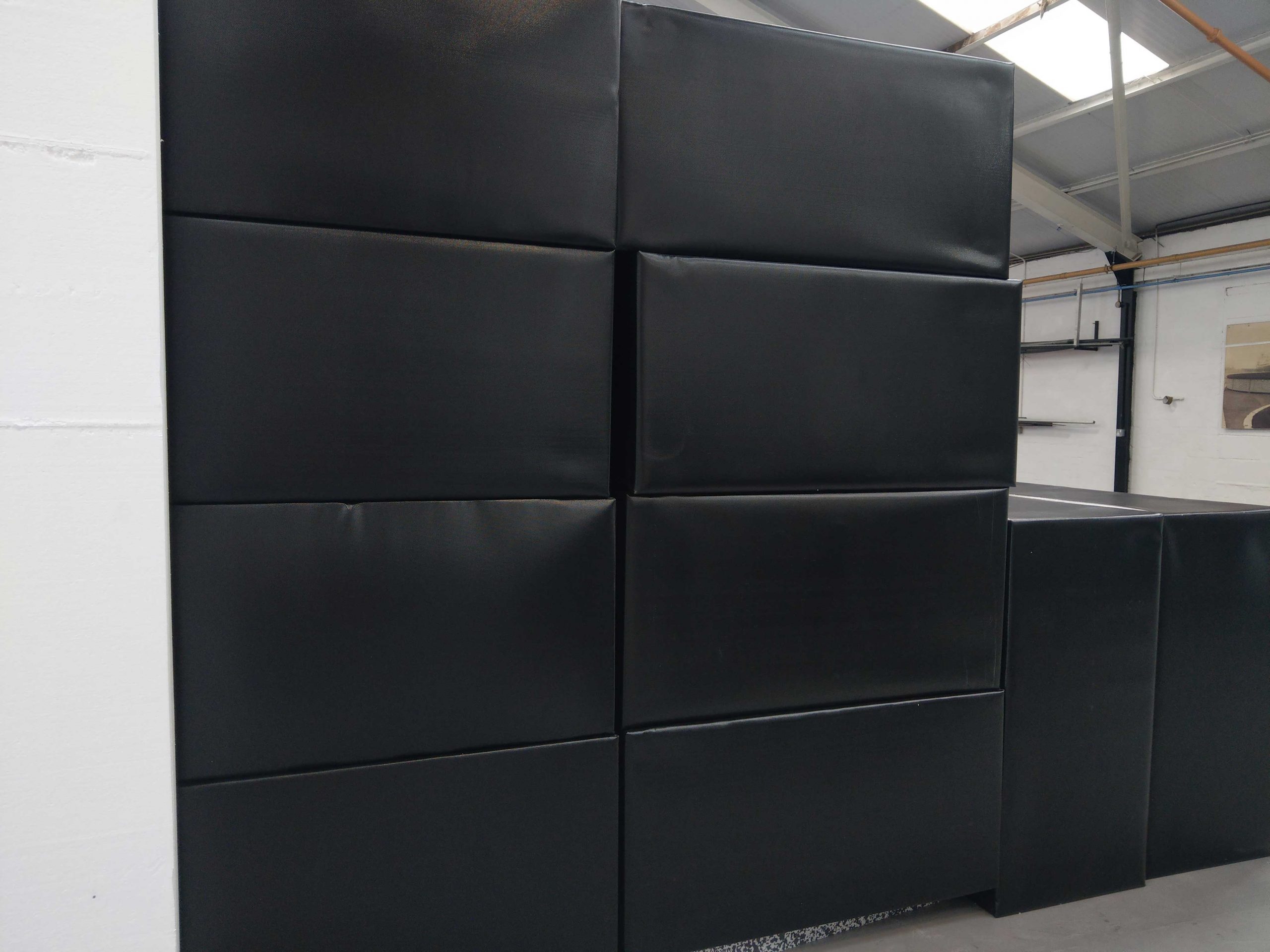
Project: Encapsulated Polystyrene Infill Project, Supply & install EPS wrapped blocks to three road bridge arches in London.
Client: F M Conway
Summary:
The encapsulation of Expanded Polystyrene blocks with a hydrocarbon-resistant membrane inside a three-arched road bridge.
• The installation of Landflex 100ES to the floor and walls of the arches to 1.2m below the soffit.
• Installation of Landflex 100ES welded to the wall section to ensure total encapsulation of EPS blocks
• Total encapsulation of individual EPS blocks in our factory to enable completion of the final 1.2metres
Challenges: Working in restricted areas with limited space. The challenge was to provide a solution to the completion of the EPS installation without compromising risk to the contractor or installation teams.
Our Solution: Our Landflex 100ES material is a chemically resistant flexible membrane and the preferred choice for this project due to its chemical resistance, tensile strength and flexibility. It’s designed for longevity in challenging environments. The road bridge at Lisson Grove is expected to settle by 10mm, exerting pressure on the EPS installation. The combination of lightweight EPS blocks and the chemical resistance of our Landflex 100ES will ensure the integrity of the project for the future.
The installation comprised 296 individually wrapped EPS blocks, pre-wrapped off site in our Billericay factory; utilising a total of around 5,800m2 of material. Each block measured 2.4m x 1.22m x 600mm and the whole project was completed in 38 days (22 days manufacturing, 16 days on site).
Search for
Recent Blogs
Categories
- Attenuation linings(4)
- Case Study(3)
- Drinking Water(9)
- EPS Block Wrapping (Encapsulated Polystyrene Blocks)(2)
- Gas Barrier & Gas Venting(12)
- Landfill & Environment(7)
- Petrochemical Containment(6)
- Reed Beds(3)
- Reservoirs, Lakes & Canals(12)
Archives
- November 2022 (1)
- June 2022 (52)
- August 2016 (2)
- April 2015 (1)
- March 2015 (1)